The design and development process is a critical journey that shapes the creation of products, systems, or services. Throughout history, this process has evolved to incorporate new technologies, methodologies, and insights. In the year in 999, a time characterized by medieval innovation and craftsmanship, the phases of design and development were influenced by societal needs, available materials, and cultural practices. This article delves into the multifaceted stages of the design and development process as understood in that era, examining how ideas transitioned from conception to reality.
Understanding the Context of 999
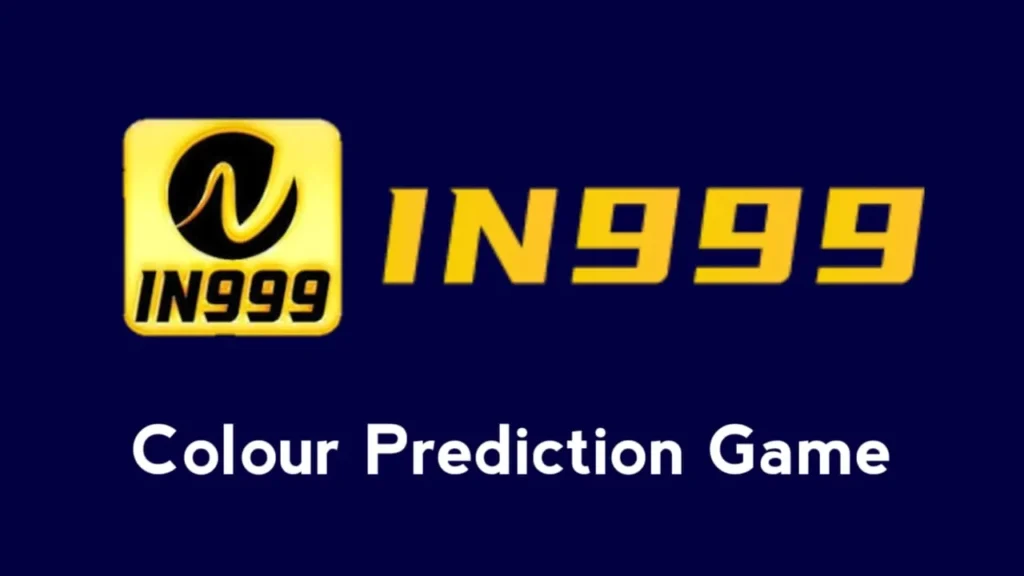
Social and Cultural Influences
In the year 999, Europe was experiencing significant social and cultural shifts. The feudal system was in place, influencing how resources were allocated and labor was organized. This societal structure affected the availability of craftsmen who were skilled in various trades necessary for product development.
Artisans were often linked to local guilds, which played crucial roles in regulating quality and techniques used in design and production. Craftsmanship flourished in this context, leading to distinctive regional styles and innovations. The collaboration among artisans within these guilds fostered an environment ripe for creativity and shared knowledge.
Technological Landscape
The late first millennium was a period of gradual technological advancement. Innovations such as the heavy plow and water mills began to take root, reshaping agricultural practices and providing surplus resources. These advancements fueled the growth of towns and urban centers, where trade and commerce thrived. Such changes not only enhanced the quality of life but also created opportunities for the development of more complex products.
As metalworking techniques improved, artisans began to experiment with designs that incorporated intricate patterns and functionalities, resulting in items ranging from simple tools to elaborate decorative pieces. The evolution of construction methods also played a part in architectural design, contributing to the iconic structures we associate with medieval times.
Economic Factors
The economy in 999 was largely agrarian, yet it was beginning to transition towards a more market-oriented system. The rise of trade routes facilitated exchanges between different regions, which in turn brought about exposure to diverse materials and techniques. This increased demand for craft goods led to more focused design and development processes aimed at meeting specific consumer needs.
Artisans had to consider both functionality and aesthetics in their creations, balancing these two aspects while remaining mindful of economic constraints. The evolving marketplace thus significantly impacted the way products were designed, developed, and distributed.
See more: in999
Phases of the Design Process

Ideation and Conceptualization
The process of design begins with ideation, where artisans and designers brainstorm ideas based on societal needs, available resources, and personal inspiration. During this phase, they would draw upon historical knowledge, folk traditions, and current trends to develop innovative concepts.
Research and Inspiration
Artisans often sought inspiration from nature, religion, and mythology, which played integral roles in medieval society. Religious motifs, for instance, found their way into various artifacts and structures, serving both decorative and symbolic purposes. Understanding the cultural context and historical precedents became vital for the creation of meaningful designs.
Sketching and Prototyping
Once a concept was established, artisans frequently moved into sketching their ideas. Although written documentation was limited, visual sketches helped convey thoughts and facilitated communication among guild members. With rudimentary materials, they created prototypes to test functionality and aesthetics, allowing them to refine their initial ideas before full-scale production commenced.
Artisans relied on direct experience and trial-and-error methods to evaluate the feasibility of their designs. Prototypes offered valuable insights that could lead to iterative improvements, ensuring the final product met both artistic and practical standards.
Planning and Resource Allocation
After refining the design, careful planning ensued to ensure adequate resource allocation. This involved selecting appropriate materials, estimating costs, and determining labor requirements. Given the limitations in transportation and access to certain resources, artisans had to be strategic in their sourcing to minimize waste and maximize efficiency.
Material Selection
Choosing the right materials was critical in the design process. Artisans in 999 utilized locally sourced resources—wood, metals, textiles, and ceramics—tailored to their geographic location. For example, wood from nearby forests might be favored for furniture design, while iron might be preferred for weaponry or tools.
Understanding the properties of these materials allowed artisans to employ them effectively, enhancing durability and functionality in their creations. Additionally, experimentation with different material combinations could yield unique textures and finishes that elevated the aesthetic appeal.
Labor Management
The successful execution of a design required skilled labor. Artisans often collaborated with other members of their guilds, pooling expertise to complete complex projects. Labor management included assigning tasks according to individual strengths, ensuring that each artisan contributed effectively to the overall process.
Training apprentices was another vital aspect of labor management. By nurturing the next generation of craftsmen, guilds preserved traditional techniques while encouraging innovation through fresh perspectives. A well-organized labor force ultimately ensured high-quality output and efficient workflow.
Production and Quality Control
With the plans in place, the production phase commenced. This stage involved translating designs into tangible products through skilled craftsmanship. Quality control was paramount; artisans took pride in their work and strived to maintain consistent standards.
Craftsmanship Techniques
Artisans employed various techniques, from hand-carving to weaving, depending on the type of product being developed. Each technique required specialized skills and deep knowledge of the materials involved. Mandated by guild regulations, artisans adhered to best practices to ensure their work met established quality benchmarks.
The production process often entailed multiple iterations, where artisans refined their techniques based on feedback and observations. Continuous learning and adaptation were key components in developing a reputation for excellence within the community.
Testing and Final Adjustments
In the pursuit of perfection, testing the functionality and durability of crafted items was essential. Artisans examined finished products for flaws and made adjustments as needed. This scrutiny extended beyond the physical attributes of the product; artisans also considered how well the item fulfilled its intended purpose.
Feedback from potential users or fellow craftsmen played an influential role during this stage. Engaging with clients offered a channel for further refinement, ensuring the end product resonated with the target audience.
Development and Launch
Market Introduction
Once the product reached its final form, the next phase involved introducing it to the market. Effective marketing in 999 relied heavily on word-of-mouth, local gatherings, and merchants showcasing goods in bustling marketplaces.
Community Engagement
Artisans often showcased their creations at local fairs and festivals, interacting directly with potential buyers. These events served as platforms for artisans to demonstrate the functionality of their products while sharing stories behind their designs, creating emotional connections with prospective customers.
Community engagement was vital for building relationships and establishing a loyal customer base. Local patrons were likely to patronize those whose craftsmanship they trusted, reinforcing the importance of reputation in the success of any launch.
Strategic Partnerships
Forming partnerships with merchants or other craftspeople could enhance visibility and accessibility to wider audiences. Merchants acted as intermediaries, distributing products beyond local markets and facilitating trade across regions. Collaborations with other artisans in different trades also encouraged cross-pollination of ideas and materials, resulting in innovative products.
Feedback and Iteration
Following the market introduction, gathering feedback from consumers became central to the ongoing development process. Listening to customers’ experiences provided invaluable insights that informed future iterations and enhancements.
Consumer Insights
Artisans welcomed input regarding the usability and desirability of their products. Observing how consumers interacted with their creations allowed artisans to identify areas for improvement, whether related to functionality, comfort, or aesthetics. Understanding consumer preferences became a guiding principle for subsequent designs.
Continuous Improvement
In the spirit of continuous improvement, artisans adapted their processes based on feedback received. Whether tweaking a design feature or altering production methods, embracing change allowed them to remain relevant in an ever-evolving market.
This adaptive approach fostered innovation and kept artisans ahead of competitors, ensuring they maintained a solid foothold in their communities.
FAQs
What were some common materials used in the design and development processes in 999?
Wood, metals such as iron and bronze, textiles, and ceramics were commonly used materials. Artisans selected materials based on availability, functionality, and aesthetic appeal.
How did artisans in 999 collaborate on designs?
Artisans typically belonged to guilds where they shared knowledge and expertise. Collaboration often involved brainstorming sessions, knowledge-sharing workshops, and joint projects that leveraged each member’s unique skill set.
What role did guilds play in the design process?
Guilds regulated craftsmanship standards, provided training for apprentices, and fostered a sense of community among artisans. They enabled craftsmen to learn from one another, preserving traditional techniques while encouraging innovation.
How did feedback influence product development?
Feedback allowed artisans to understand consumer needs and preferences, informing adjustments to product design and functionality. This iterative approach led to continuous improvement and refinement of future products.
What was the significance of aesthetics in the design process of 999?
Aesthetics played a crucial role in attracting consumers and conveying cultural values. Artisans incorporated decorative elements that reflected local traditions, beliefs, and artistry, creating products that resonated with their communities.
Conclusion
The design and development process in the year 999 was a dynamic interplay of creativity, craftsmanship, and community. Artisans navigated through phases of ideation, planning, production, and launch, all while adapting to societal needs and market demands. Their dedication to quality and innovation laid the groundwork for future generations of craftsmen, demonstrating the enduring legacy of creative expression and functional design. As we reflect on these historical phases, we recognize the timeless principles that continue to guide the design and development process today.